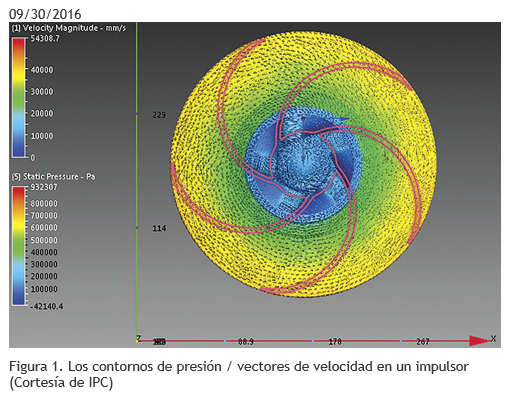
La tecnología de maquinaria rotativa juega un papel importante en la industria de la producción. Las condiciones del proceso de la planta son a menudo severas. Una unidad de acabado de tamaño típico puede proporcionar una capacidad de producción de 1500 toneladas por hora.
Los puntos críticos del proceso, como los de las bombas de carga de hornos que se enfrentan a temperaturas cercanas a los 800° C, requieren soluciones tecnológicas especiales. Una planta de craqueo catalítico fluido (FCC) requiere que la alimentación se mezcle con el catalizador y luego se bombee al reactor con temperaturas de alrededor de 500° C. El aire requerido por el proceso es normalmente suministrado por compresores centrífugos o axiales con un flujo normal de alrededor de 50,000 metros cúbicos normales por hora (Nm3/h). Los requisitos de energía también pueden alcanzar varios megavatios. La maquinaria rotativa para aplicaciones de compresión y bombeo juega un papel crítico en la determinación de la robustez general de la planta. Las bombas centrífugas, presentes en casi todos los procesos de la planta, son especialmente importantes.
El mercado de las bombas centrífugas cubre una larga gama de aplicaciones de procesos de producción. Se han desarrollado muchas configuraciones de bombas centrífugas para diferentes aplicaciones, que incluyen una o varias etapas, división axial o radial y posición del rotor horizontal o vertical.
Las bombas horizontales son las más comunes en aplicaciones de proceso. Se utilizan en una amplia gama de presiones (hasta 400 bares) y temperaturas (hasta 450° C), mientras que las bombas verticales se utilizan para una gama más restringida de aplicaciones, principalmente en condiciones de baja altura neta de succión positiva disponible (NPSHA) y temperaturas muy bajas.
Los reglamentos técnicos y las normas de la industria son actores principales en la industria de maquinaria rotativa. Los códigos 610 del American Petroleum Institute (API) y del Hydraulic Institute proporcionan pautas amplias y completas que impulsan todo el proceso de producción de la bomba. Estos estándares cubren la mayoría de los aspectos desde la ingeniería inicial hasta la etapa de fabricación en el taller. API 610 ha sido sujeto a revisiones, y los criterios para evaluar la eficiencia de la bomba se movieron de las tolerancias previas sobre la eficiencia a las tolerancias reales impuestas a la potencia total adsorbida. Los límites de vibración tenían modificaciones análogas, lo que refleja los esfuerzos para lograr ciclos de vida de la máquina más largos y mejores eficiencias energéticas.
Mejoras en bombas centrífugas
La búsqueda continua de la dirección de la planta por la competitividad del mercado final ha impulsado el desarrollo de la tecnología de bombas centrífugas en términos de rendimiento y reducción general de costos. La evolución de la tecnología de materiales metálicos ha jugado un papel importante. Durante el funcionamiento, las bombas están sujetas a corrosión, erosión y fatiga. Desde una perspectiva de diseño, es necesaria una selección de material adecuada para una vida útil satisfactoria de la máquina.
La tecnología de materiales actual promueve una mejor resistencia a las condiciones adversas. Los procesos metalúrgicos reales tienen un mejor control de la química de los materiales, como es el caso de los aceros dúplex (CD4MCu) o grados de acero especiales como el endurecimiento por precipitación 17-4-PH que se usa a menudo para ejes. En otros casos, los procesos innovadores como los recubrimientos por plasma o láser para el endurecimiento de la superficie de la manga permiten una mejor resistencia al desgaste. El desarrollo de métodos informáticos de elementos finitos (FEM) también promueve una mejor comprensión del campo de tensión dentro de los componentes de la bomba. El diseño moderno de maquinaria rotativa aprovecha la disponibilidad de herramientas de software que permiten evaluaciones delicadas en puntos de diseño mecánico temáticos, como la selección de rodamientos, pistones de equilibrio y dimensionamiento de holguras de manguitos. Estos elementos, y las condiciones operativas del diseño de límites, contribuyen a la estabilidad final del rotor.
Otro problema bien conocido que afecta a las bombas centrífugas es la cavitación. Este fenómeno se caracteriza por la vaporización del fluido que se produce cuando la presión neta es menor que la presión de vapor. La recuperación de la presión aguas abajo hace que las burbujas de vapor implosionen repentinamente, lo que produce picaduras que pueden dañar el impulsor. Los efectos de la cavitación pueden ser dramáticos, desde la degradación del rendimiento hasta la falla total.
En el pasado, los operadores de bombas expertos solían detectar la cavitación reconociendo el ruido característico. Los avances recientes en el estudio de vibraciones muestran que la cavitación entrante también se puede detectar usando armónicos (transformada rápida de Fourier o FFT), abriendo la puerta a un diagnóstico automatizado. El enfoque tradicional del problema de la cavitación se basa en el dimensionamiento de la planta con un margen de seguridad estático para la altura de succión positiva neta requerida (NPSHR) en el punto operativo.
Es posible controlar la cavitación midiendo la presión, la temperatura y la velocidad del fluido en el punto de succión de la máquina más cercano. En el pasado, se utilizaron sistemas de monitoreo instalados permanentes en un número limitado de casos. Algunos determinaron que el costo del sistema de monitoreo era excesivo, especialmente para máquinas pequeñas. La llegada al mercado de controladores lógicos asequibles ha cambiado esto y, en la actualidad, incluso las bombas centrífugas pequeñas pueden beneficiarse de estos sistemas de control y supervisión.
Otro elemento que ha contribuido constantemente a la mejora de la tecnología de bombas es el desarrollo de métodos de prueba. La disponibilidad comercial de sistemas avanzados de medición de vibraciones permite la adquisición de una cantidad considerable de datos. Las sondas de proximidad y los transductores de velocidad corporal permiten a los ingenieros de pruebas ejecutar investigaciones detalladas sobre el comportamiento vibratorio de la maquinaria y encontrar correlaciones entre los parámetros mecánicos, las lecturas de flujo, el rendimiento, los componentes armónicos del espectro de FFT, las formas de la órbita y fenómenos específicos como la cavitación o la pérdida de rotación del flujo interno.
La introducción de la dinámica de fluidos computacional (CFD) también influyó en el desarrollo de la industria de bombas de proceso. El diseño hidráulico de los patrones de flujo de la bomba utilizando formas tridimensionales es una tarea delicada. El aumento de la potencia computacional y la disponibilidad de códigos confiables permitieron mejoras consistentes en el proceso de diseño de bombas centrífugas y la integración de la experiencia del fabricante de equipos originales (OEM) con simulaciones y predicciones confiables. Los códigos comerciales modernos de CFD tienen capacidades avanzadas para modelar fluidos viscosos e no viscosos. También ofrecen varias ecuaciones de turbulencia y algoritmos no estacionarios para regiones giratorias de turbomáquinas.
El ciclo de diseño completo aún debe cerrarse con las pruebas físicas finales de la máquina en los talleres OEM, pero la implementación de métodos CFD conduce a mejores diseños y tiempos de respuesta más cortos. La simulación por computadora permite a los fabricantes de equipos originales desarrollar rápidamente formas de canales hidráulicos optimizadas para objetivos específicos (como la eficiencia máxima o NPSHR) en las condiciones operativas especificadas por el usuario final. La importancia de estos avances se hizo aún más evidente a la luz de la posibilidad de fabricar piezas hidráulicas personalizadas obtenidas del diseño CFD mediante la integración con la tecnología moderna de diseño asistido por computadora o fabricación asistida por computadora (CAD / CAM).
Sistemas de control
El avance en los sistemas de control es otra área de desarrollo importante para la tecnología de bombas. Los datos sobre las industrias europeas muestran que la mayor parte del uso de energía se destina a aplicaciones de accionamiento de bombas. En entornos industriales, los accionamientos de bombas utilizan alrededor del 76 por ciento de la energía total. A pesar de este costo considerable, la idea de un sistema de control para bombas de baja potencia no ha sido popular en el pasado, especialmente en comparación con bombas más grandes donde actualmente se utilizan sistemas de control avanzados. Esto se debe principalmente a la baja relación de beneficios / costos de las bombas pequeñas causada por el alto impacto que tendría un sistema de control en el costo general de la estación de bombeo.
Un enfoque de OEM en el pasado era proporcionar múltiples piezas de repuesto junto con la instalación. Este tipo de enfoque basado en redundancia requiere mayores costos de instalación inicial para múltiples bombas. En este caso, muchas bombas funcionan hasta su destrucción. El costo de mano de obra y reemplazo no se calcula en el diseño preliminar de la planta, pero se incurre durante la operación. Hoy en día, la instalación de un sistema de control dedicado puede ser beneficiosa incluso para bombas pequeñas o de baja potencia. Es posible obtener grandes ahorros de energía integrando un sistema de variador de frecuencia (VFD). Se pueden lograr ahorros considerables adicionales en operación y mantenimiento mediante el uso de sistemas avanzados de control de autodiagnóstico.
Los sistemas de control de bombas modernos implementan la idea de una automatización completa de las bombas utilizando el número mínimo de sensores de campo instalados. Este objetivo se puede lograr mediante el uso de modelos basados en el rendimiento (PBM), que ahora son posibles gracias a la mayor capacidad computacional de los sistemas comerciales de controladores lógicos programables (PLC). Este sistema proporciona funciones de autodiagnóstico, protección y control de la máquina.
En comparación con una instalación no supervisada, los sistemas supervisados con costos de instalación ligeramente más altos pueden reducir los costos de mantenimiento, los costos de reparación y el tiempo de inactividad de la producción.
Las principales características y ventajas de este tipo de sistemas son las capacidades de control multivariable, VFD y PBM. El usuario establece el parámetro de proceso que se va a controlar y el sistema proporciona un monitoreo continuo de todos los parámetros de proceso relevantes. Cambia automáticamente el control sobre los parámetros que requieren intervención de protección. En comparación con los métodos de regulación tradicionales, los VFD permiten grandes reducciones en la cantidad de energía utilizada, así como una mayor eficiencia energética.
La disponibilidad de PBM permite a los usuarios predecir el rendimiento esperado en las condiciones operativas reales. Las mediciones de campo les permiten determinar el rendimiento real. La comparación del rendimiento esperado y las mediciones reales permite al sistema proporcionar indicaciones de autodiagnóstico (anomalías particulares como alteración de la cavitación, degradación mecánica o falla de los transmisores) y activar acciones de protección correlacionadas.
Muchas tendencias en tecnología de bombas evolucionan continuamente. Muchos OEM continúan investigando y desarrollando la integración de CFD y CAD / CAM con el objetivo de crear nuevos diseños de bombas de alta eficiencia. La adopción de estos dos métodos permitirá diseños personalizados optimizados para cada aplicación única. En comparación con los métodos tradicionales de selección de bombas basados en procedimientos de selección de catálogo, este proceso de diseño personalizado permitiría a los usuarios finales encontrar las soluciones de mayor eficiencia para sus aplicaciones. Se espera que la difusión de nuevos sistemas de control con PMB y la implementación de algoritmos de software de autodiagnóstico proporcionen beneficios adicionales. La integración de VFD para una mejor administración de energía operativa proporcionará ahorros de energía, reducción de costos de mantenimiento y mayor tiempo de actividad. Esta integración de estos métodos es clave para el funcionamiento exitoso de las bombas centrífugas de próxima generación.
Por Massimiliano Di Febo y Pasquale Paganini de IPC